This article explores the answer to the question “What is Lean Six Sigma?”, detailing its core principles and the significant benefits it offers to organizations aiming for operational excellence. It explains how Lean Six Sigma combines the waste reduction focus of Lean with the quality improvement tools of Six Sigma to drive efficiency and effectiveness. KPI Fire’s Lean Six Sigma Software is highlighted as an essential solution that integrates these methodologies, providing your organization with powerful tools to manage continuous improvement programs and achieve strategic goals.
Introduction: What is Lean Six Sigma?
Lean Six Sigma is a data-driven methodology that combines the efficiency of Lean principles with the quality focus of Six Sigma. Lean and Six Sigma are respectively and historically defined as two separate methodologies that can be categorized under the umbrella term of Business Improvement. More recently, these two methodologies have been merged into a common philosophy and referred to as one: Lean Six Sigma.
By eliminating waste, reducing defects, and optimizing processes, organizations can significantly enhance performance, customer satisfaction, and bottom-line results. The adoption and application of Lean Six Sigma principles empower businesses to achieve sustainable growth and gain a competitive edge.
Alternatives to Lean Six Sigma
While Lean Six Sigma is a popular methodology for process improvement, there are other effective approaches to achieving and sustaining business improvement. With KPI Fire, you can implement all of the following business improvement methodologies in addition to LSS:
- Total Quality Management (TQM): Focuses on overall organizational improvement and customer satisfaction.
- Lean Manufacturing: Emphasizes eliminating waste in production processes.
- Kaizen: Promotes continuous improvement through small, incremental changes.
- Theory of Constraints (TOC): Identifies and eliminates constraints in a system.
- Business Process Management (BPM): Improves business processes through analysis, design, and optimization.
- Agile: Delivers value through iterative development and flexibility.
- Benchmarking: A process of comparing a company’s performance to industry best practices.
- Root Cause Analysis (RCA): A problem-solving technique that identifies the underlying cause of a problem.
- Kanban: A visual system for managing workflows that focuses on visualizing the work, limiting work in progress, and continuously improving.
- Design Thinking: A human-centered approach to problem-solving that emphasizes empathy, ideation, and prototyping.
The best choice depends on your specific goals, business processes, team skills, and organizational culture.
Historical Background: Origins of Lean and Six Sigma
The history of Lean and Six Sigma can be traced back to the early 20th century, with significant contributions from both the United States and Japan. Henry Ford’s introduction of the assembly line in 1913 revolutionized manufacturing, and while Ford laid the groundwork, Toyota took these concepts further. Enter the Toyota Production System (TPS), which is the foundation of Lean as we know it today. The term “lean” was only officially coined in the 1980s by researchers at the Massachusetts Institute of Technology, who deemed Toyota’s approach to be far more significant than others.
As a close concept to Lean, although developed on its own, Six Sigma was pioneered by Bill Smith at Motorola in the 1980s. The company was facing increasing competition and quality issues, leading Smith to develop a rigorous methodology to improve product quality and overall business performance. The name “Six Sigma” is derived from statistical process control, representing a process that produces only 3.4 defects per million opportunities. This level of quality was the ambitious goal set by Motorola.
Core Principles of Lean Six Sigma
At its core, Lean Six Sigma emphasizes eliminating the 8 wastes and improving efficiency. Below, we review core Lean Six Sigma principles or foundations that make up a “House of Lean” and what they entail for organizations across multiple industries.
- Waste elimination: Visualizing the entire process with Value Stream Mapping to identify waste and inefficiencies.
- Continuous Improvement: Fostering a culture of ongoing process enhancement and improving efficiency.
- Holistic & Employee Driven: Engaging employees in the improvement process.
- Customer Focus: Understanding and meeting customer needs and expectations.
- Defects Reduction: Minimizing errors and defects in products or services.
By adhering to these principles, organizations can significantly enhance their operations, reduce costs, and improve customer satisfaction. Lean emphasizes eliminating waste and improving efficiency.
What is Six Sigma? Understanding its Focus
Six Sigma is a data-driven methodology that aims to improve the quality of business processes by identifying and eliminating defects and minimizing variations. It’s a structured approach to problem-solving that uses statistical methods and a set of tools to achieve significant process improvement.
- Reducing Defects: The primary goal is to minimize errors and defects in products or services.
- Process Improvement: Enhancing the efficiency and effectiveness of business processes.
- Data-Driven Decision Making: Relying on statistical analysis and data to guide problem-solving.
- Customer Satisfaction: Ultimately, improving customer satisfaction by delivering higher quality products or services.
By employing a systematic approach and focusing on measurable results, Six Sigma has been successfully implemented in various industries to enhance productivity, reduce costs, and increase customer loyalty.
Continuously Improve With Our Latest News & Updates
Lean vs. Six Sigma: Understanding the Differences
Lean Six Sigma is a powerful combination of two methodologies that complement each other to drive significant process improvement. While Six Sigma focuses on reducing variation and defects, Lean emphasizes eliminating waste and improving efficiency. Consider the video below to fully grasp the differences between these closely related terms. We would also recommend brushing up on essential lean concepts and terms to supercharge your greater understanding.
Key Steps for Integrating Lean into Six Sigma
By integrating Lean principles into the Six Sigma framework, organizations can achieve accelerated results and a more holistic approach to process optimization.
1. Align Strategic Goals:
- Clearly define the organization’s strategic objectives.
- Ensure Lean Six Sigma initiatives align with these goals.
2. Build a Strong Foundation:
- Leadership Commitment: Secure top-level support for the initiative.
- Culture Change: Foster a culture of continuous improvement and employee involvement.
- Training: Provide comprehensive training in both Lean and Six Sigma methodologies.
3. Identify Improvement Opportunities:
- Conduct a thorough process assessment using Lean tools like value stream mapping.
- Prioritize opportunities based on their potential impact and feasibility.
4. Combine Lean and Six Sigma Tools:
- Use Lean tools such as value stream mapping and 5S to identify waste and process inefficiencies.
- Apply Six Sigma tools such as DMAIC and statistical analysis to eliminate defects and reduce variation.
- Consider a hybrid approach, combining tools from both methodologies as needed.
5. Pilot Projects:
- Implement Lean 6 Sigma projects on a smaller scale to test the approach.
- Analyze results and make adjustments as needed.
6. Expand and Sustain:
- Replicate successful projects across the organization.
- Establish a Lean Six Sigma infrastructure for ongoing improvement.
- Embed Lean Six Sigma principles into the company culture.
Key Integration Points:
- Value Stream Mapping: Use it to identify waste and then apply Six Sigma tools to eliminate root causes.
- DMAIC: Incorporate Lean principles into the Define and Measure phases to focus on customer value and process flow.
- Kaizen: Use Lean’s continuous improvement philosophy to sustain Six Sigma gains.
Kaizen in Lean Six Sigma
Kaizen, meaning “continuous improvement” in Japanese, is a fundamental principle underpinning Lean Six Sigma. Kaizen in Lean Six Sigma could be described as the philosophy of making small, incremental changes to processes and systems over time. Kaizen in Lean Six Sigma serves as the cultural backbone, fostering a mindset of constant improvement among employees at all levels. It complements the structured DMAIC methodology by providing a more organic approach to problem-solving.
Key Tools and Techniques in LSS
A variety of tools and techniques are used within the Lean Six Sigma framework to eliminate waste and reduce defects. Here’s a breakdown of some of the most commonly used ones in each phase of DMAIC.
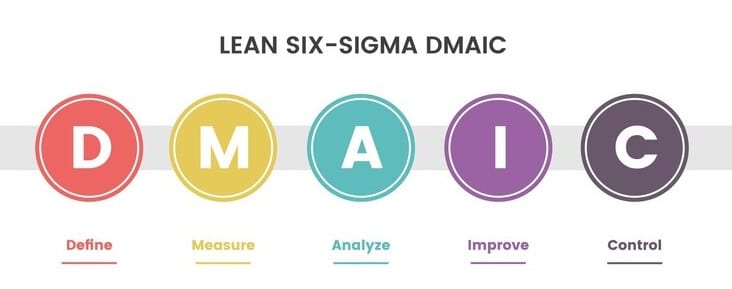
Define Phase
- Customer Segmentation: Identifying different customer groups and their specific needs.
- Voice of the Customer (VOC): Understanding customer expectations and requirements.
- Project Charter: Outlining project goals, scope, and deliverables.
- SIPOC: Defining the Supplier, Input, Process, Output, and Customer.
Measure Phase
- Process Mapping: Visualizing the process flow to identify potential issues.
- Data Collection: Gathering relevant data to understand the process performance.
- Capability Analysis: Assessing the process’s ability to meet customer requirements.
- Statistical Process Control (SPC): Monitoring process stability and identifying abnormalities.
Analyze Phase
- Cause and Effect Diagram (Fishbone Diagram): Identifying potential root causes of a problem.
- Five Whys: Drilling down to the root cause of a problem through repeated questioning.
- Data Analysis: Using statistical methods to analyze data and identify patterns.
- Correlation Analysis: Determining relationships between variables.
Improve Phase
- Design of Experiments (DOE): Identifying factors that significantly impact a process output.
- Poka-Yoke: Implementing error-proofing measures to prevent defects.
- Standard Work: Documenting best practices for consistent performance.
- Value Stream Mapping: Identifying value-added and non-value-added activities.
Control Phase
- Statistical Control Charts: Monitoring process performance over time and identifying deviations.
- Standard Operating Procedures (SOPs): Documenting standardized work instructions.
- Audit: Verifying adherence to the new process and identifying areas for improvement.
Remember: The choice of tools and techniques depends on the specific project and its requirements. A successful Lean Six Sigma implementation involves a combination of these tools and a thorough understanding of the methodology.
Benefits of Lean 6 Sigma for Organizations
Lean Six Sigma, as a powerful methodology, empowers organizations to achieve exceptional performance by generating various benefits. Consider the varying and intertwining benefits of lean six sigma for organizations in more detail below.
Financial Benefits
Implementing Lean Six Sigma in organizations potentially leads to significant cost reduction. By eliminating waste and inefficiencies, organizations can significantly reduce operational costs. Similarly, changes in revenue increase count as another benefit, whereby improved quality and customer satisfaction can lead to increased sales and market share. In terms of financial benefits, profitability enhancement cannot be understated, whereby the combined impact of cost reduction and revenue growth drives higher profitability.
Operational Benefits
Lean Six Sigma delivers significant organizational benefits to organizations. By streamlining processes and reducing cycle times, it boosts efficiency and productivity. Simultaneously, it enhances product or service quality through defect reduction. Ultimately, meeting customer needs and expectations more effectively fosters increased loyalty. Moreover, by proactively identifying and addressing potential issues, Lean Six Sigma strengthens overall business resilience.
Organizational Benefits
Lean Six Sigma offers substantial organizational benefits. It cultivates a data-driven culture, empowering informed decision-making and continuous improvement. By involving employees in process enhancement, it boosts morale and engagement. Moreover, it serves as a platform for developing problem-solving and leadership skills, fostering talent growth.
Ultimately, Lean Six Sigma equips organizations with superior quality, efficiency, and customer focus, driving a significant competitive advantage. By implementing Lean Six Sigma, organizations can achieve a holistic transformation that impacts the bottom line, customer satisfaction, and overall business performance.
Leveraging KPI Fire’s Lean Six Sigma Software
KPI Fire lean management software offers a robust platform to streamline and optimize your improvement initiatives. By providing a centralized hub for data collection, analysis, and project management, KPI Fire DMAIC Process Software empowers organizations to efficiently execute the DMAIC methodology. With its intuitive interface and built-in templates, teams can easily collaborate, track progress, and measure the impact of their Lean Six Sigma projects.
Key features such as real-time dashboards and visual management tools facilitate data-driven decision making and ensure transparency throughout the organization. Ultimately, KPI Fire’s software helps businesses accelerate their Lean Six Sigma journey and achieve sustainable performance improvements.
KPI Fire offers a comprehensive suite of tools designed to accelerate improvement initiatives. Its core features include:
- KPI & Data Management and Analysis: Centralized data repository, powerful analytics, and visualization capabilities to identify trends, root causes, and opportunities for improvement.
- Project Management: Robust project management tools to structure and track Lean Six Sigma projects, including task assignment, timelines, and resource allocation.
- DMAIC Workflow: Built-in templates and workflows to guide teams through the DMAIC methodology, ensuring consistency and efficiency.
- Collaboration: Real-time collaboration features to foster teamwork and knowledge sharing among project members.
- Reporting and Dashboards: Customizable reports and dashboards to monitor project progress, measure performance, and communicate results to stakeholders.
By leveraging these capabilities, organizations can streamline their Lean Six Sigma processes, improve data-driven decision making, and achieve measurable results faster. Be sure to request your demo of KPI Fire today to leverage it in favor of Lean Six Sigma initiatives and discover the benefits it may bring to your organization.