Innovation in business is at an all time high. Staying competitive requires constant evolution and a strategy for continuous improvement. To thrive, organizations need a culture that constantly strives for excellence – a culture of continuous improvement (CI). This guide is your ultimate companion on this journey.
Join us as we unveil an all-rounded approach to building a robust CI program, fostering a culture of innovation and problem-solving within your team. In this guide, we attempt to answer essential questions: What does a successful CI Program look like? What is the vision for your CI program? Who owns the vision for Continuous Improvement? Why is continuous process improvement important?
Why is a Continuous Improvement Program Important?
Continuous Improvement (CI) isn’t just a nice-to-have—it’s a strategic imperative. CI is a deliberate, structured approach to business improvement that gives organizations a competitive edge. In a world of constant change, standing still puts you at a disadvantage. Your competitors are constantly evolving—if you’re not improving, you’re losing ground.
A well-defined CI program empowers organizations to adapt quickly to change, drive efficiency, and deliver higher value to customers. It creates a culture of innovation and growth—both at the organizational level and for individual employees. When employees are given opportunities to solve problems, refine processes, and contribute to meaningful change, they feel more engaged and invested,
Beyond internal benefits, CI aligns with global standards like ISO-9001, ensuring quality and consistency that meets or exceeds industry benchmarks. In some industries, CI isn’t just optional it’s a mandated requirement.
Yet, despite recognizing the value of Continuous Improvement, many companies try to pursue it without dedicated resources—relying on part-time champions or sporadic efforts. If you’re serious about improving performance, building a culture of excellence, and achieving lasting results, it’s time to assign dedicated headcount to Continuous Improvement.
Yet too many companies say they believe in CI while relying on part-time champions or ad hoc efforts to drive change. If you’re serious about improving your processes, culture, and performance, it’s time to assign dedicated headcount to Continuous Improvement.
How should a CI Program be Structured?
To every CEO/COO/CFO: “If you don’t have a VP of Continuous Improvement, YOU ARE the VP of Continuous Improvement”.
If something is important, you allocate resources to it. When you assign a resource (a person’s time) to an activity, you can expect accountability, ownership, and results. The first step to ensure that Continuous Improvement is valued, is to assign ownership.
The primary job of the Continuous Improvement (CI) function in an organization is to drive sustainable, incremental improvements in processes, efficiency, and overall performance. Continuous Improvement is not just about fixing problems but about creating a culture where employees at all levels seek out and implement better ways to work. In many organizations this role is delegated through a CFO, or COO Chief Operating Officer. In more mature organizations a CI program might have a VP of Continuous Improvement, or Operational Excellence. These roles are a good sign that the organization values this discipline.
Leading a CI program can start in a small company as a part time or partially allocated role. For example, a finance controller who was assigned to track the impact of a project might take the lead. Or a Project leader who was exposed to Lean/Six Sigma methods might take it on as a champion. As your company grows you can look to have more resources dedicated to Continuous Improvement. Depending on the size of your company some of these functions might be done by more or fewer people. In a large company with multiple regions and facilities the following functions may be present.
Owner of the Vision: A Single visionary CI leader
- This might be the CEO, or COO until a VP of CI(or equivalent) is established
- Advocate for Continuous Improvement as a Core Value at the CxO & Sr Leadership Table
- Annual Goal Setting Targets (in collaboration with operations & finance leaders)
- Quarterly Program Reviews
Core CI Team: Director(s) of CI, Regional or Multi-site, Multi Function CI Support
- Program Structure, facilitating
- Facilitate Best Practice sharing
- Mentoring Site Champions, Project Leaders, Sponsors.
Site Champions/ CI Managers
- Advocate for CI at the local/ single site, single function level
- Lead Projects
- Mentorship, train others
- Ensure CI program activities make it to front lines, and ensure front line voices are heard by leadership.
Project Leaders
- Lead improvement projects
- Use Structured Problem Solving/Best Practices to achieve key improvement projects
Project Sponsors
- Align Projects with Strategic Initiatives
- Usually are Sr Leaders, Executives, or Business unit Owners.
- How to be an Excellent Project Sponsor
Finance Role
- Ensure projects account for Financial Impact.
- Avoid “power point dollars”.
Idea Generators
- Ideas for Improvement need to come from all levels.
- These can be front line employees, leaders, managers, or senior business unit leaders.
Steering Committee (optional)
- In a large company, it may be useful to establish a Steering committee comprised of representatives from each of the roles listed above.
If your company doesn’t have separate people for these roles, you still need to do them, they just may be shared roles or people wearing multiple hats.
How should the ROI of a Continuous Improvement program be measured?
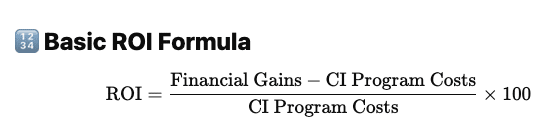
The concept of Return on Investment is quite simple. Do more of the things that make you money, and fewer of the things that don’t make money.
Unfortunately, in many businesses people neglect to do these simple calculations on a regular basis. There are far too many examples of CI programs that neglected to do the calculations. Then, when there is a leadership change, someone in charges asks “why are we spending money on this CI program”. And without tangible information and proof, the program gets cut. Don’t let this happen to your program.
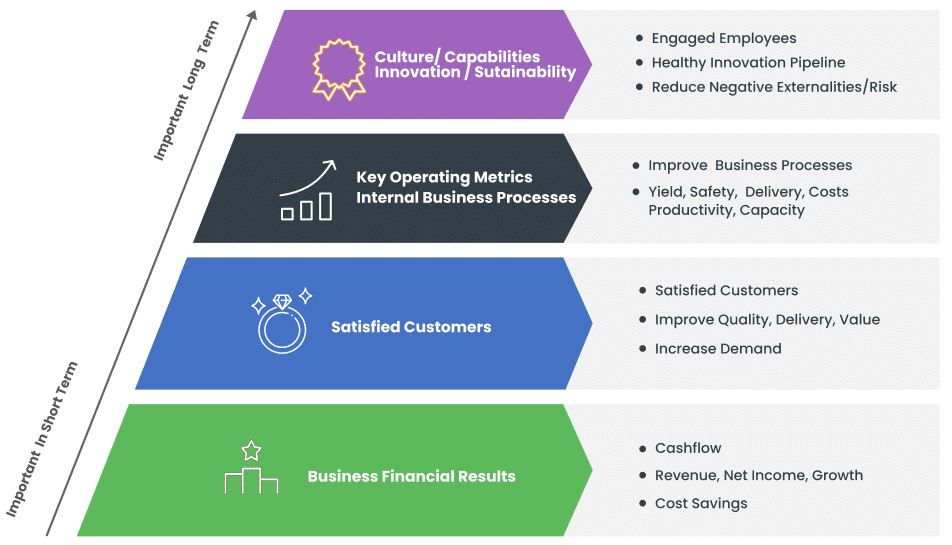
Types of Savings / Improvements
The simplest way to start thinking about savings is to think about savings on a continuum of Hard Savings vs Soft Savings, or Direct vs Indirect Savings.
- Hard Savings/Direct Savings are: the most tangible, immediate, and easily calculated savings.
- Soft Savings/Indirect Savings: These are savings that are more difficult to translate into dollars or take longer to show up as actual dollar savings.
- See this post for discussion on Hard vs Soft Savings.
- See this post for How to Manage a Cost Savings Initiative.
- See this post for discussion of Cost Savings vs Cost Avoidance.
3 Types of Project & Program Benefit that are worth Tracking
- #1: Financial Savings: These projects are directly traceable to financial impact.
- #2: Improvements in Key Operating Metrics : Safety, Quality, Delivery, Costs, Capacity, Flow time are a few examples.
- #3: Participation & Involvement: Developing the skills for improvement takes time. Nurture and appreciate the opportunities to practices skills.
How Much Hard Savings Should We Expect from Our Continuous Improvement (CI) Program?
The short answer: it depends.
The longer answer depends on several factors, including the size of your company, the maturity of your CI program, and the types of improvements or benefits you’re targeting—whether they’re operational savings, productivity gains, or strategic outcomes.
Here are some benchmarks and considerations to guide your expectations:
-
Large Enterprises ($100B+ in revenue): It’s reasonable to expect 1–3% in hard cost savings by improving current operations and increasing productivity across the organization.
-
Productivity vs. Compensation: If your organization is aiming to provide a 7% pay increase next year, you should target at least a 7% improvement in productivity to offset that cost.
-
Strategic Initiatives: For targeted improvements driven by strategic insights, the impact can be dramatic—ranging from 50% to 500% or more in returns.
Some companies treat R&D expenses as “costs of improvement” and then track benefits such as revenue from new products as part of their ROI calculations.
Resources
Who should own the Vision for the CI Program?
While Senior Leaders, VP of CI, VP of OPEX, VP of Transformation all have a stake in the CI program, ideally the vision should be co-owned by Senior Leaders and the VP of CI. Senior leaders provide the strategic direction aligning the CI program with overall organizational goals.
The VP of CI, with their CI expertise, translates that vision into actionable plans and ensures effective implementation. This collaboration fosters strong leadership and practical execution for a successful CI program.
What training should a Continuous Improvement Program include?
- Lean Six Sigma Belt training options
- How to Launch a Successful Lean/6Sigma Green Belt Training Program
- What is Waste? The 8 Wastes of Lean Manufacturing
- Which Metrics should we track to improve our business
- Change Management Training
- The Language of Continuous Improvement
- The Language of Strategic Planning
- How to be an Excellent Project Sponsor
- How to build a Winning Project Charter
What is the role of Finance Controllers in a Successful CI Program?
Finance Controllers act as the financial backbone of a successful CI program. They bring their expertise to the table in several key ways:
1. Financial Stewardship – Budgeting and Cost Control
They ensure the CI program operates within allocated funds. They might also participate in cost-benefit analyses to justify the program’s existence and secure funding for future improvements.
2. Data-Driven Decision Making – Performance Measurement
Finance Controllers design reports that track key metrics like cost savings, defect reduction, and development cycle time improvements. This data helps management assess the program’s effectiveness.
3. Risk Management – Security and Compliance
CI programs can introduce new security vulnerabilities. The controller helps identify and mitigate these risks. They ensure proper access controls and data security measures are in place. They may also advise on complying with financial regulations related to software development.
4. Integration and Communication – Financial Systems Integration
The CI program might generate financial data like usage costs. The controller facilitates the smooth integration of this data with existing financial systems for efficient reporting and analysis.
5. Bridging the Gap
They act as a bridge between finance and development teams. They translate financial information into clear and actionable insights that developers and other stakeholders can understand.
What are example job descriptions for a CI program?
Below we share some examples of job descriptions for job titles within the ideal Continuous Improvement program:
Job Description for a VP of CI?
The Vice President (VP) of Continuous Improvement is a senior executive responsible for driving a culture of operational excellence, process optimization, and strategic transformation across the organization. This role focuses on developing and executing enterprise-wide continuous improvement initiatives, leveraging Lean, Six Sigma, and other methodologies to enhance efficiency, reduce waste, and improve business performance. The VP partners with executive leadership, department heads, and cross-functional teams to align improvement efforts with corporate goals.
Lead CI initiatives, drive operational excellence, & cultivate a culture of continuous improvement across all departments. 10+ yrs exp, Lean Six Sigma preferred. Strong leader & communicator.
Job Description for a Director of CI?
The Director of Continuous Improvement is responsible for developing and leading initiatives that drive operational excellence, efficiency, and a culture of continuous improvement within an organization. This role involves implementing Lean, Six Sigma, and other process improvement methodologies to enhance productivity, reduce waste, and improve overall business performance. The Director works cross-functionally with leadership and teams to align improvement initiatives with strategic objectives.
Direct CI strategy, lead process improvement initiatives, & build a high-performing CI team. 7+ yrs exp, Lean Six Sigma a plus. Strong analyst, leader & communicator.
Job Description for a Manager of Continuous Improvement
The Manager of Continuous Improvement is responsible for leading process optimization efforts inside of an organization/site/location, fostering a culture of continuous improvement, and driving operational excellence. This role typically involves using Lean, Six Sigma, and other continuous improvement methodologies to streamline processes, reduce waste, and enhance efficiency. The Manager collaborates with cross-functional teams to identify opportunities for improvement and implement sustainable solutions.
What are some red flags that my CI program is at risk?
- No Financial metrics: If your CI program does not track savings/impact on CI projects, it is only a matter of time before your budget is cut and your program is terminated.
- Lack of Senior Leadership Support: Do your Senior leaders pay attention to your CI Program? Do they show up to training events? Do they participate in aligning CI projects with Strategic goals? Do Senior leader set targets for Cost Savings or Productivity Improvements?
- Lack of Business Unit Leader Support: Business Unit or function leaders are typically the ones with decision making authority to allow people on their teams to spend time on improvement activities or not. If business unit leaders do not make time available for improvement, there will likely be a constant “fire fight” feeling in a department. People may be running ragged to keep up.
- Low Employee Engagement: Is there a lack of excitement or participation in CI initiatives? Are employees resistant to change or hesitant to submit continuous improvement ideas?
- No Time Allocation: Your organization says CI is important, but there is no time allocated in the unit level plans to implement changes.
- Stagnant Progress: Are you stuck in a rut? Is there a lack of measurable improvement or progress on CI projects?
- Misaligned Goals: Do your CI goals align with the overall company or business strategy? Are CI efforts focused on the right areas for improvement?
- High Turnover in CI Team: Is there a revolving door in your CI team? This can indicate frustration or a lack of clear direction.
- Focus on Blame: Does your CI program point fingers instead of fostering a collaborative problem-solving environment?
- Inconsistent Implementation: Is the continuous improvement process inconsistently applied across different departments or projects? This creates confusion and undermines the effectiveness of the program.
- Just Checking the Box: Are CI initiatives seen as a box-ticking exercise rather than a genuine effort to improve?
What is the life cycle of a CI Program?
A Continuous Improvement (CI) program follows a cyclical process with these key stages:
- Initiation: Identify areas for improvement, set goals, and secure resources.
- Planning & Design: Develop a roadmap, identify processes to improve, and establish measurement methods.
- Implementation & Execution: Run pilot projects to test methods, implement improvements, and monitor progress.
- Evaluation & Review: Analyze results, identify further improvement areas, and celebrate successes.
- Continuous Improvement: Standardize best practices and continuously seek new areas for improvement.
Throughout the life cycle, key roles play their essential parts in ensuring the success of the CI program as follows.
Senior Leaders should:
- Connect to important KPIs
- Explain the Strategic Connection
- Reiterate the importance of the work
- Celebrate the impact
- Show up to reviews
Directors of CI should:
- Invite senior leaders to reviews.
- Communicate that they are training, and need constituents to be there to show that this is important to them.
CI Managers should:
- Collaborate with senior leaders to identify areas for improvement within the organization.
- Work with teams to set SMART goals.
- Provide ongoing opportunities for Coaching & Mentoring.
- Oversee the implementation of pilot projects prior to collection and analysis of data.
Site Champions should:
- Support Needs Assessment
- Promote Program Goals
- Participate in Pilot Projects
- Spread Best Practices
DMAIC vs PDCA for Structured Problem Solving?
Structured Problem Solving is one of the core pillars in Continuous Improvement. Structured problem solving is a systematic approach to identifying, analyzing, and resolving problems in a way that leads to sustainable improvements. Instead of jumping to quick fixes or assumptions, structured problem solving follows a defined process to understand the root cause and implement effective solutions.
What should a CI Project Review look like?
A CI project review should assess the program’s impact on achieving strategic goals like faster releases and higher quality. It dives into metrics like build success rate and lead times. Review areas for improvement and opportunities to minimize waste, like reducing rollback rates or improving test coverage. Aim for a balance between celebrating achievements and identifying areas to strengthen your CI for long-term success.
10 Questions to CRUSH Your Next Project Review
1. What is the problem we are looking to solve, or the opportunity we are trying to capture?
Start every project review by revisiting the why. This question reminds everyone of the purpose behind the project, ensuring alignment and helping to refocus if the team has strayed from the original intent.
2. What is the target condition or goal of this project?
Frame your goals clearly using this structure: “From X to Y by when.” For example, “Increase customer retention from 65% to 75% by the end of Q3.” This clarity helps track progress and keeps the team goal-oriented.
3. What progress has been made since our last review?
Evaluate how far you’ve come. Have milestones been achieved? Celebrate wins, identify areas of stagnation, and understand what’s working well or not.
4. What do we plan to accomplish before our next review?
This forward-looking question sets the stage for the next phase of work. Clarify upcoming assignments, who owns them, and the expected outcomes to maintain accountability.
5. What is the health of this project?
Use a color-coded system to evaluate project health:
Green: On schedule, on budget.
Yellow: Some issues, but recovery is possible.
Red: Significant problems affecting delivery scope, benefits, or timeline.
Discuss the reasoning behind the status and, if necessary, action plans for improvement.
6. Are we on schedule? Are there any delays?
Timelines are crucial. Assess whether you’re meeting deadlines and identify reasons for delays. This discussion can surface blockers or inefficiencies that need immediate attention.
7. What risks are being monitored? Are there any new or escalated risks?
Projects rarely go exactly as planned. Review known risks and determine whether new risks have emerged or existing ones have intensified. Discuss mitigation strategies to stay ahead of potential issues.
8. Do we need to adjust? Are there any changes? Is the prior project plan still relevant?
Projects evolve. This question ensures that your plan adapts to changing circumstances. If adjustments are necessary, discuss how they affect timelines, budgets, or deliverables.
9. Is the team properly engaged? Are stakeholders properly engaged?
Review the team’s involvement and capacity. Are they motivated and clear on their roles? Additionally, assess whether stakeholders are providing the necessary input and support. Engagement gaps can derail progress if not addressed.
10. How will we manage changes to project definition or deliverables?
Changes are inevitable, but how you manage them can determine a project’s success. Define a clear process for handling changes, ensuring transparency and alignment among all stakeholders.
What are good Strategic Goals for a CI Program?
- Increased Competitiveness
Enhance the organization’s ability to compete in the market. This could involve reducing costs, improving product quality, or becoming more efficient in delivering services.
- Improved Customer Focus
Increase customer satisfaction and loyalty. Examples include reducing lead times, improving product features based on customer feedback, or streamlining the customer service experience.
- Enhanced Employee Engagement:
Foster a culture of continuous improvement where employees feel empowered to identify and implement improvements. This can involve providing training in problem-solving methodologies, encouraging participation in CI initiatives, and recognizing employee contributions.
- Streamlined Processes:
Identify and eliminate waste and inefficiencies in processes. This could involve streamlining workflows, reducing cycle times, or improving communication between departments.
- Data-Driven Decision Making:
Increase reliance on data to inform improvement efforts. This involves establishing metrics to track progress, analyzing data to identify root causes of problems, and using data to guide future improvement initiatives.
Note: When setting CI program goals, it’s crucial to ensure they are SMART goals (Specific, Measurable, Achievable, Relevant, and Time-bound). This ensures your goals are clear, well-defined, and attainable within a specific timeframe.
What Metrics should a CI Program Track?
CI programs benefit from tracking metrics that measure different aspects of the development process. Here’s a breakdown of key metrics to track:
Cost Reduction:
- Reduced Waste: Track waste reduction in areas like materials, time, and rework. This could involve metrics like:
- Scrap Rate: Percentage of raw materials wasted during production.
- Downtime: Time when equipment is not operational.
- Rework Rate: Percentage of products requiring rework due to defects.
- Inventory Optimization: Track inventory levels and turnover to identify and reduce unnecessary holding costs. Metrics could include:
- Average Inventory Days: Average number of days raw materials or finished products sit in inventory.
- Inventory Turnover Rate: Number of times inventory is sold and replaced within a period.
- Process Efficiency: Track improvements in process times and resource utilization to reduce labor and overhead costs. Metrics could include:
- Cycle Time: Average time it takes to complete one unit of production.
- Labor Productivity: Units produced per labor hour.
Margin Improvement:
- Increased Throughput: Track the number of units produced or services delivered per unit of time. This directly impacts sales volume contributing to margin. Metrics could include:
- Production Units per Hour: Number of units produced in an hour.
- Customer Throughput Time: Average time it takes to fulfill a customer order.
- Improved Quality: Reduced defects and rework lead to higher quality products, potentially allowing for higher selling prices. Metrics could be:
- Defect Rate: Percentage of products with defects.
- Customer Satisfaction: Measures customer perception of product quality.
- Reduced Lead Time: Faster time to market allows for quicker revenue generation and can improve overall margins. Metrics could include:
- Order to Delivery Lead Time: Time from order placement to product delivery.
The Ultimate Continuous Improvement Program: Wrapping Up
Remember, the continuous improvement cycle is a never-ending journey. As your organization evolves and new challenges arise, so too will your CI program. Embrace the ongoing cycle of learning, adaptation, and growth, and watch your organization reach its full potential through effective continuous improvement management.
Where the emphasizes is placed on the importance of clear goals, measurable progress, and a culture of collaboration – KPI Fire excels in all of these areas. Request a free demo and witness firsthand how KPI Fire can transform your CI program, starting today.